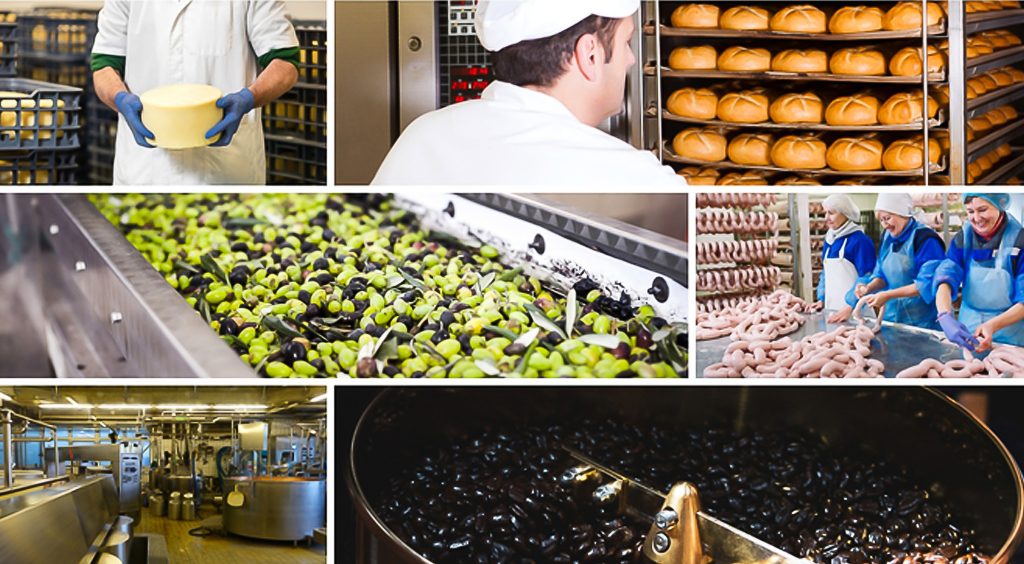
Preventing Contamination During Food Production
Contaminated products strongly affect your bottom line, not only by causing mistrust among consumers, but also with costly recalls, public warning letters, and FDA audits. Failing to follow GMPs can result in bad press and even lawsuits or a shutdown of your facility.
Preventing different types of contamination spread through the air is defined not only on an efficient HVAC system, but more importantly, how efficient the air filtration design and its operation is.
A dedicated air cleaner within the food industry should be specialized to handle these types of specific environments, along with following cleaning and risk analysis protocols. Standard industrial air filtration systems may clean certain types of particles efficiently but fail in other safety categories that may compromise the machine itself and/or the plant’s operations.
Air filtration for food production, storage, and distribution
QleanAir Scandinavia has developed the FS 70 FG; a completely new, redesigned air filtration system specifically for the food and beverage industry.
The design follows relevant standards within the industry regarding Hazard Analysis & Critical Control Points (HACCP), including guidelines on the design to be impermeable towards cleaning, cleaning agents, and liquids.
The FS 70 FG essentially improves hygiene practices within the food production chain in reducing the emergence and spread of airborne contaminations.
Highlights of the FS 70 FG
- Custom, multi-filter configuration: Meeting ISO 16890 and EN1822 filter standards ensuring continuous efficiency in capturing a wide range of dust/airborne particles. With multiple filter layers the FS 70 FG creates a safety net should an accident occur and the first filter becomes damaged.
- Hygienically designed: All surfaces are smooth and made out of non-porous materials to be easy to clean. Crevices have been minimized to avoid spaces where particles and contaminants can gather.
- Seamless, rounded edges: All gaskets, seals and joints are smooth to avoid organic material from collecting, and able to withstand aging and detergents.
- Leak-resistant unit housing: The hull of the unit is completely sealed, avoiding any leakage of particles or contaminants into the unit as well as to avoid for any pests being able to invade the hull.
- Corrosion-resistant materials: A uni-frame hull made with austenitic stainless steel 316L / ISO 1.4404.
- Food grade seals and gaskets: All gaskets and seals are smooth and continuous to avoid organic material from collecting. They are also able to withstand aging from disinfectants and detergents. Materials comply with EC1935/2004 – approved for food and drinking water contact.
- Constant airflow regulation: Ensures constant airflow in combination with mechanical filtration, guaranteeing the performance of the unit over time.
- Accessories: Optional hoods, and anti-microbial, fabric ducting systems/textile diffusers.
- Optimized service: Included, routinely scheduled service plan, i.e. filter replacement.
Investing in your air quality pays off
For more detailed information on the FS 70 FG, click here. You can also visit our Food and Beverage page to learn about the different areas of food production we help protect.